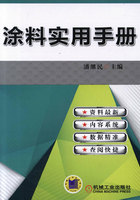
1.10 涂料在生产和储存中常见问题及解决方法
1.10.1 发浑
1.现象
发浑也称浑浊、发混、发糊,是指清漆、清油或稀释剂由于不溶物析出而呈现的云雾状不透明的现象。例如,在开罐后,清漆、油性清漆和合成树脂清漆表现为透明度差、浑浊,甚至出现沉淀。
2.原因
1)稀释剂选择不当或用量过多。清漆是胶体状物质,其贮存稳定性主要取决于各种成膜物质在溶剂中的溶解度,如果溶剂种类选择不当,则部分涂料不易溶解,就会发浑。
2)涂料所用的溶剂或成膜物质中含有水分。水分的存在会促进催干剂析出,造成浑浊。
3)贮存时间过长或温度不适宜。
4)催干剂选择不当,特别是选用铅类催干剂,在稍有水分或低温时就会使清漆变浑浊。
5)漆质不良、性质不同的两种清漆混用。
3.解决方法
1)可以加入一些松节油或芳烃溶剂来改善稀释剂,即根据成膜物质的不同来选用合适的稀释剂。例如,对于使用溶剂过量的慢干清漆,可加入少许松节油;对于快干清漆(如硝基清漆),可加入少量丁醇或苯类芳烃溶剂。
2)在涂料生产过程中必须除去稀释剂中的水分。丙酮、乙醇、醇类可用分馏法分离;苯类、汽油、松节油可用分层法分离。溶剂桶在贮存时要盖严,以防止水分进入桶内,还要避免在雨天和湿度大的气候条件下施工。如果清漆出现浑浊,则可用加热的方法排除水分,也可将桶放平,使水分自然沉降到桶底,然后排除。
3)改善涂料贮存条件,避免将涂料存放在温度过高或过低的场所,并在贮存有效期内使用涂料。清漆贮存温度最好不低于20℃,还需将涂料桶放置在木架上以防降温。如果清漆略有浑浊,一般可照常使用。如果发浑得较严重,可用水浴加热至60~65℃,注意加热时切不可用明火加热,并要防止水汽的混入,但也不能完全盖严桶盖。
4)选择合适的催干剂。对于醇酸清漆,可采用钴、锰、铁的复合催干剂,也可采用环烷酸钴或锰等,尽量不用铅类催干剂,还需注意催干剂的用量要随油的不饱和度的增加而减少。对于醇酸树脂,催干剂中一般可加入质量分数为0.04%~0.06%的钴和质量分数为0.3%~0.5%的铅。
5)尽量不要将不同种类的清漆混合使用。
6)若清漆发浑严重、无法补救时,只能调腻子用,或降级使用,甚至报废。
1.10.2 沉淀和结块
1.现象
沉淀也称沉底或沉降,是指涂料在贮存过程中,其固体组分下沉至容器底部的现象。结块是指当沉淀现象严重时,涂料中的颜料、体质颜料等颗粒沉淀成用搅拌方法不易再分散的致密块状物。当涂料开桶后,用一搅拌棒插入涂料桶中,提起时,若具所黏附的涂料颜色和稠度均一,则无沉淀;若上稀下稠,底物有难以搅动的感觉,即出现沉淀。当搅拌棒无法插到桶底,底部沉淀硬结,无法搅拌均匀时,则是出现结块。常见的易沉淀涂料品种有红丹漆、防污漆、防锈漆(如云母氧化铁防锈漆)和低性能乳胶漆等。
2.原因
1)清漆类沉淀,多数是杂质、不溶性物质或铅类催干剂等在存放时由于低温或受潮而被析出。
2)色漆沉淀多数为使用的颜料相对密度大、粒子粗(分散不良)、体质颜料用量大(涂料的颜基比过大)所致。
3)稀释剂加入过多,使涂料黏度偏低,涂料失去了正常的表面悬浮状态,颜料和填料产生沉淀。
4)贮存温度过高,某些颜料和树脂在漆中的悬浮性能被破坏,使涂料黏度降低而沉淀结块。一般涂料的贮存温度以15~25℃为宜。
5)贮存时间过长,超过了涂料的保质期。色漆如果贮存时间过长,颜料和填料因密度大,会沉降到容器底部,最终形成硬结。有些树脂也发生类似现象。
6)颜料与涂料树脂之间产生某种化学聚合反应或相互吸附,引起凝胶,产生沉淀。
3.解决方法
1)清漆类沉淀、结块可采用过滤或加热的方法处理。
2)在设计涂料配方时选用合适的颜基比,一般不要超过2∶1。尽量选用密度小些的颜料和填料,有些颜料(如红丹粉、铬黄、云母氧化铁、铁红、沉淀硫酸钡等)密度较大,可用少量的低密度颜料和填料替代。
3)在涂料中加入防沉剂,利用少量助剂的特殊性能制成触变性涂料,以改变涂料的悬浮状态。常用的防沉剂有硬脂酸系列、气相二氧化硅、改性膨润土和氢化蓖麻油等。
4)选用的颜料和填料之间不能相互反应。锌粉、铝粉、氧化锌等比较活泼,在贮存稳定性不佳的涂料中尽量不用或分罐包装。涂料的黏度不能过低。在涂料生产时,应尽量研磨分散均匀,以达到规定的黏度、细度。
5)涂料贮存应放置在阴凉通风处,定期将涂料桶横放、倒置或摇动几次。要注意涂料的贮存期限,先入库的先使用,对于一些贮存期限低的涂料(如氯化橡胶、氯乙烯、聚氨酯类涂料)尤其要注意。
6)对于已沉淀的涂料,可搅拌均匀后再使用。对于结块现象,应先把可流动部分倒出,用刮铲从容器底部铲起沉淀并研碎,再把流动部分倒回原桶中,充分混合后再使用。若仍有干结沉淀,只能报废或降级使用。
1.10.3 结皮
1.现象
结皮是指涂料在容器中,由于氧化聚合作用,在液面上形成皮膜的现象,主要表现为涂料开罐后,在其表面覆盖一层黏稠胶皮类物质,下面涂料仍然均匀。
2.原因
1)涂料中催干剂加入过多、涂料含有过度聚合的桐油较多、色漆过稠或颜料和填料含量较高。
2)包装容器密封不好,或容器内装载的涂料量少,留有较大的空间被大量的空气占据所致。
3)存放时间过长或存放温度过高。
4)施工过程中漆料长时间暴露在空气中,或使用后剩余的漆料未密封好,容器内有较大的空间。
3.解决方法
1)调整涂料配方时,可暂时少加或不加促进表面干燥的催干剂,待施工前再按比例调入。在生产配方中,可加入0.1%~0.3%(质量分数)的防结皮剂,如邻甲氧基酚、苯酚、邻苯二酚、松节油、丁醇和环己酮肟等。
2)涂料桶尽量装得满一些,并在上面加一些稀释剂(如松节油等),使存留的空气少一些,但不能太满,应留有一定的空间,防止因天热而发胀。若有条件,可在涂料装桶后把留下的部分空气抽掉,然后灌入一些惰性气体。
3)为防止结皮,剩余的少量涂料,应用密闭小号容器盛放。可在涂料上放一层牛皮纸或添加一层挥发较慢的溶剂(如松节油),并把盖子盖紧达到密封要求。
4)加快涂料周转,避免涂料长期存放。贮存处应通风,避免高温。
5)对已经形成的结皮应小心地剔除,余下的下层涂料经搅拌和过滤后仍可继续使用。
1.10.4 变色
1.现象
变色是指涂料在贮存过程中,由于某些成分的化学或物理变化或者与容器发生化学反应而偏离其初始颜色的现象。最常见的是在开启色漆桶时出现颜色不符,如绿色涂料开桶后竟是蓝色的,或色漆开桶后是清漆,复色漆出现颜色悬浮等。
2.原因
1)涂料配方设计时,各种树脂与颜料和填料的相容性不好,出现浮色现象。
2)色漆中的颜料发生化学反应。例如,含有铁蓝的蓝色涂料或草绿色涂料,由于容器内空气不足,铁蓝发生还原作用而褪色;铁蓝和钛白、氧化锌、锌钡白等制成的涂料,在贮存过程中发生还原作用等。
3)复色漆中颜料密度不同,密度小的颜料上浮,大的下沉。例如,由铬黄和铁蓝配成的绿色涂料,铁蓝上浮呈蓝色而铬黄容易下沉。
4)涂料中由于某些组分之间相互反应,如金粉、铝粉和清漆会发生作用,从而失去金属光泽,色彩变绿、变暗。
5)涂料中的某些组分与包装铁桶发生反应。例如,虫胶漆在马口铁[1]桶中颜色会变深,贮存越久颜色越深且发黑;硝基涂料在铁桶中会变褐色等。某些溶剂(如酯类)极易水解,与铁容器反应使颜色变深,特别是白色漆最为明显。
3.解决方法
1)在涂料生产过程中要避免水汽的混入,并适当延长分散研磨时间,同时加入少量的润湿分散剂,以防止浮色现象。分散剂加入量通常为0.2%~1%(质量分数),一般是进口助剂,如硅油、聚丙烯酸酯类、高分子聚羧酸盐、多氨基酰胺膦酸酯、脂肪醇硫酸酯等,应根据具体颜料用量和品种而定。
2)用铜粉或铝粉作颜色的涂料,由于涂料中的游离酸对铝粉、铜粉有腐蚀作用,所以会使涂料变黑或发绿。可通过选用中性涂料,生产的时候在最后阶段加入铜粉、铝粉来解决。最好是把金属颜料与涂料分罐包装,使用时随时调配。
3)包装容器的铁皮桶要镀锌或镀锡,有些特殊涂料最好用塑料桶或瓷罐、玻璃瓶等包装,如虫胶清漆和硝基清漆要用非金属容器贮存。
4)当复色漆颜色不一致时,经充分搅拌均匀,颜色仍能恢复一致。若经搅拌均匀,与空气接触后,颜色可恢复原色,则不属于真正的变色。
1.10.5 发胀
1.现象
发胀是指涂料的黏度显著增加,直至变为厚浆状、胶体或硬块的现象,在形态上又表现为假厚(假稠)、胶化和肝化等形式。
(1)假厚 也称为假稠或触变。涂料看来外表稠厚,但一经机械搅拌就能流动自如,停止搅拌后又恢复如初的现象。
(2)胶化 涂料从液态变为不能使用的固态或半固态的现象,如细的颜料粒子结成块粒状,黏度增高,结成胶冻状。
(3)肝化 涂料必须经过过量稀释后才能使用或仍难以使用,如涂料黏稠,无法搅动,呈硬胶状,形状类似肝块。
2.原因
1)假厚现象通常出现在含颜料成分较高的涂料中,尤其以滑石粉、氧化锌、锌钡白和红丹粉等最为明显。
2)所用颜料与基料树脂起反应。例如,金粉和铬黄等颜料容易造成硝化纤维素涂料出现肝化;酸价高的涂料和盐基性颜料在贮存过程中起皂化反应,红丹、锌白、铅白与天然树脂相遇而产生肝化。
3)胶体的基料分散相大部分带正电荷,与带负电荷的颜料混合时易出现胶化和凝固。例如,酸性的炭黑能使氨基树脂涂料产生胶化。
4)容器不完全密闭或未装满,在贮存过程中部分溶剂挥发,使涂料浓缩、增稠。空气中的氧也能促进胶化。
5)水分的混入对酸性漆料和碱性颜料的反应有促进作用,容易造成涂料的肝化或胶化现象。
6)涂料贮存温度过高也易出现肝化、胶化等现象。
3.解决方法
1)对于假厚现象,用木棒强力搅拌即可。
2)有些漆基应避免选用盐基性颜料,可以用锌钡白、钛白和氧化锑等颜料替代。若清油与红丹粉等自行调配,需当天配制当天使用。
3)一般出现肝化的涂料,轻微时可加入相应的稀释剂调稀使用,但只能作底漆,如果用来罩面会失光。无法再继续使用的,应降级或报废。
4)对于出现凝胶现象的涂料,如果是由于油料聚合过度,则经过机械搅拌作用可以重新分散,或加入少量有机酸(安息香酸)可恢复正常。涂料轻微胶化时,一般经加入同种稀释剂并用力搅拌,胶化的涂料会重新转变为均匀液体。桐油胶化时,在短期内经加入3%(质量分数)的甘油并加热即可恢复原状。如果胶化严重且不可逆时,只能报废或调腻子用。
5)涂料桶一定要密闭。如果开桶,最好在2~3天内用完。对于已结皮胶化的部分可过滤除去并降级使用。
6)在涂料生产中应避免水分的混入。因此,在湿度大的情况下尽量不要生产涂料。对某些易吸水的颜料和填料,可在阳光下晾晒或用加热烘干等方法除去水分,同时防止溶剂内水分的混入。
7)要在15~25℃的条件下贮存涂料,不要放置在日光下、散热器或火炉旁。
1.10.6 变稠
1.现象
变稠是指涂料在贮存过程中,由于组分之间发生化学反应或由于稀释剂的损失而引起的稠度增高(不一定增加到不能使用的程度)、体积膨胀的现象。
2.原因
1)漆料聚合过度,或漆料酸值过高与碱性颜料发生反应。
2)稀释剂选用不当(如沥青漆用200号溶剂汽油稀释会使沥青漆变稠),或涂料酸性太强,与碱性颜料发生了皂化反应等。
3)涂料(指溶剂型涂料)中含有水分或使用了含有较多水溶性盐的颜料。
4)聚氨酯类固化剂与空气中的潮气发生反应。
5)涂料桶漏气、漏液,造成涂料贮存期间溶剂挥发,带来变稠现象。
6)涂料贮存时间过久、温度过高,会造成涂料中树脂的进一步聚合而析出,因此也会引起变稠。当温度过低时,水性乳胶漆往往变稠,甚至结冻成块。
3.解决方法
1)涂料在生产和贮存各个环节中都要避免混入水分,生产时还要严格控制好漆料的聚合度、颜料和填料的水分、水溶性盐等指标。
2)醇酸、氨基漆加入适量的丁醇可降低黏度。
3)经常检查涂料包装桶是否密封,防止聚氨酯固化剂与空气接触而发生反应,防止溶剂挥发。
4)水性乳胶漆可移入暖房贮存2~8天,让其解冻复原。
5)对漏气、漏液的涂料桶需更换,同时加入适量的溶剂,搅拌均匀后再密封贮存。氨基烘漆贮存后变稠,可在溶剂中用至少质量分数为25%的丁醇调稀。
6)尽快在贮存有效期内用完涂料。贮存时需防止温度过高或过低,控制温度在15~25℃之间。对因冬季气温低而结冻变稠的乳胶漆,可将其移入温暖的室内2~3天,让其自然解冻;或将乳胶漆连同包装浸入热水中,让它自行缓缓解冻。解冻后的乳胶漆必须在短时间内用完,不宜再贮存起来。
1.10.7 起料
1.现象
起料也称有粗粒,是指色漆在贮存过程中呈现出的粗颗粒(即少许结皮、凝胶、凝聚体或外来粗粒)。例如,涂料开罐后,发现涂料溶液中形成颗粒状突起、漆粒子变粗。这种现象常常出现在氯化橡胶厚浆涂料和沥青涂料中。粗颗粒的存在不仅会影响涂膜外观,有时还会在喷涂作业中堵塞喷嘴。
2.原因
1)涂料生产时,如果厚浆涂料温度超过40℃,则易使颜料颗粒流变析出。
2)涂料在生产或贮存中有水汽混入,引起颜料颗粒集结。
3)颜料过粗、容器不干净或细碎漆皮带入。
4)某些树脂和颜料之间发生反应,使颜料颗粒凝结析出。
3.解决方法
1)如果厚浆涂料的温度在35~40℃,需冷却后使用,仍有粗粒则返厂研磨。
2)在涂料中适当加入阻聚剂,防止涂料在过高或低温度条件下贮存时聚合变粗。
3)生产时防止加入带有水分的溶剂,同时不要在湿度大的天气生产。颜料和填料必须处于干燥状态,如果用手攥成团而不能恢复为松散粉状,则说明颜料和填料含水过多,应烘干或在阳光下晒干。
4)适当延长研磨时间和过程,严格控制颜料和填料的颗粒细度。
5)起料现象轻微的涂料,可在充分搅拌后按要求先用80目以上筛子过滤,然后使用。起料现象严重的,需返厂重新研磨。
1.10.8 胖听
1.现象
胖听是指涂料在贮存过程中,由于桶内溶剂的气化,所造成的容器变形的现象,主要表现在铝粉涂料、锌粉涂料和某些聚氨酯涂料中。这种现象严重时会造成涂料罐自燃、起火、爆裂。
2.原因
1)涂料在高温情况下贮存,桶内温度过高,溶剂逐渐变成气态,使密封桶缓慢膨胀。
2)涂料若含有铝粉、锌粉或聚氨酯类,铝粉与涂料中的游离酸反应产生了氢气,使涂料桶变形。
3)涂料中有游离酸及水存在,贮存时间过久发生了化学反应,产生气体。
3.解决方法
1)避免在高温情况下贮存。若出现胖听现象,应立即将涂料桶移到远离涂料存放点的阴凉通风处,还可用凉水冷却,注意避开火源。开罐时可先用利器捅一小孔,缓缓将气体放掉。如果出现大量白色烟雾,则应戴上防毒面具。开罐后将涂料搅拌均匀,若无肝化、胶化现象,一般可继续使用。
2)铝粉或锌粉涂料应分罐包装,随用随配。对聚氨酯涂料,可加入1%~2%(质量分数)的二丁基月桂酸锡等助剂。
3)涂料生产时控制树脂的酸价,避免水的混入。